In our long term working at our client operation site, we found there are 7 most common piling roller bit failure as follow:
- Bearing Stuck
- Cone Inner Circle Wearing Out
- Lost Cone
- Snapped Inserts
- Inserts Quick Wear out
- Lost Inserts
- broken snapped leg
And there are 4 factors to determine when and how the piling roller bit will fail:
- Roller Bit Quality (BIT)
- Welding Method (WELDING)
- Operation (OPERATION)
- Formation Challenge (FORMATION)
Let us dive deep and see how these factors fact the performance of roller bits. And most important, what we can do to increase the performance to reach higher piling efficient and lower cost.
1. Bearing stuck
2 situation:
A. almost all the bearing is stuck and no turning.

All the roller bit bearing is stuck. This is only 1 possibility, that when the operator put the core barrel down. A hit of bottom happened. Then all the roller bit bear too much weight, suddenly all the cone will be stuck. (OPERATION).
B. Part of the cones stuck ( less than 30%)

Roller Bit Grease System Problem (BIT)
- No grease System
- Not enough grease
- Bad grease quality
There is a tiny space between the leg bearing and cone. The grease is filled inside, and function as to reduce the friction of the bearing. Good grease stickiness is more consistent, not too much vary according to the temperature.
If the grease is bad or not enough grease, the bearing will have much higher friction, and the friction will make the cone and leg expand to fill up the tiny space, and the leg and cone will be attached to come 1 part. This causes the stuck.
Bad Welding (WELDING)
Not enough cooling during the welding will break rubber seal and grease. Failed grease or leak will make the bearing stuck.
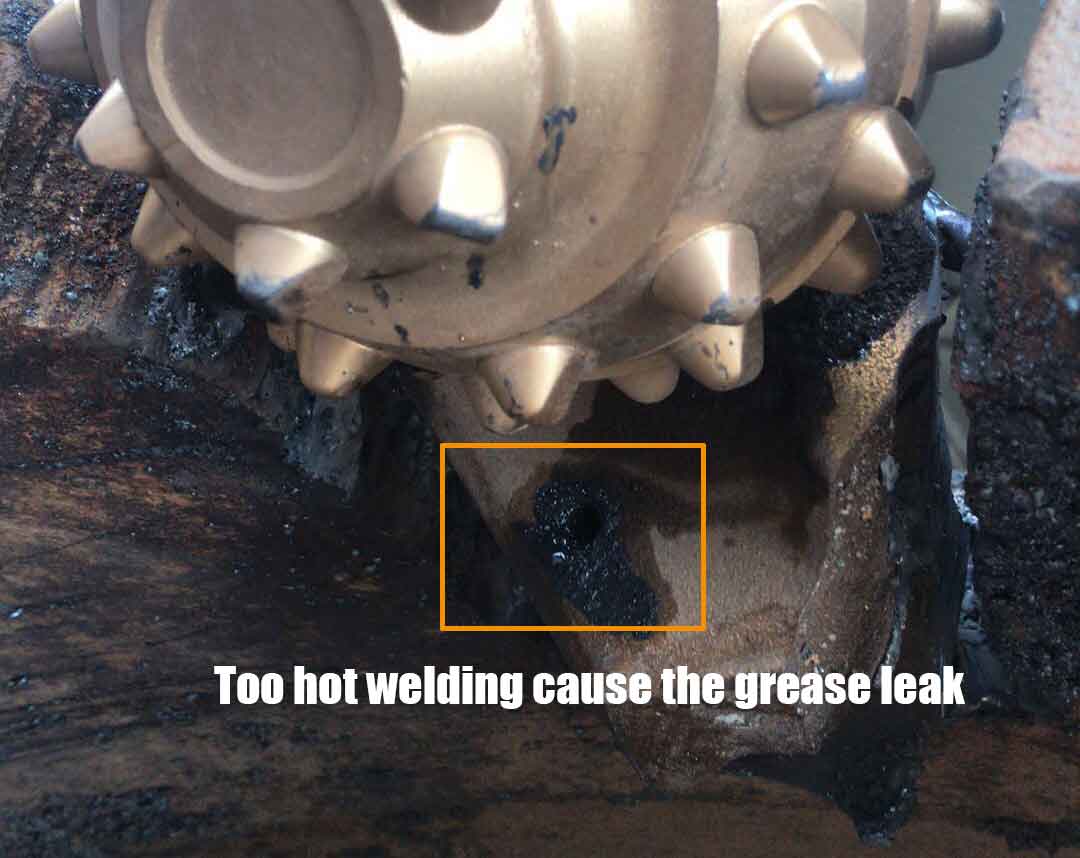
Inappropriate Operation ( OPERATION)
Pushing too much Drilling weight ( right drilling weight is 3-6 ton) and too high drilling speed will make the roller bit too hot to damage the grease and sealing, cause the bearing stuck.
Challenging Formation (FORMATION)
When the formation fracture is bad. The cutting debris can cover the roller bit to prevent the cooling and make bearing stuck. ( This can be solved with specially designed core barrel, leave us a message for more information.)
2. Cone Inner Circle Wearing Out

Bad Welding (WELDING)
The wrong positioning in the welding will cause the inner part wear out.

The inward and outward roller bit are too much overlapped. The inward roller bit inner part without the outward bit protection. The inner part will finish quick.
Caused by "Stuck Bearing"
The roller bits in the core barrel are highly depended with each other. They are integral one part. When the outward roller bit stuck, the top will wear out quickly. Without the right protection, inward roller bit inner part wear out often happens.
This is why you always see the two problems coexist at the same time.

3. Lost cone

Bad roller bit quality (BIT)
The fit clearance between the cone and bearing is ultra important. If the machining tolerance is not qualified, it will much likely to lose cone.
Operation
Too fast drilling speed will make the sealing premature failure, cause losing cone. Take 1000 mm, for example, the right rotary speed is 8 rd/min at the beginning, when the pump figure stable, which means the bottom surface got even, take 16 rd/min. ( The rotary speed related drilling weight and formation a lot, please set according to your unique application).
Too much welding hot
As almost mentioned, if the welding get too hot, damages sealing O-ring, dust will come inside the bearing and cause quick lost cone easily.
Formation
When it comes to the plastic formation, it will have a force to draw back the bit, likely to cause lost cone.
4. Snapped inserts
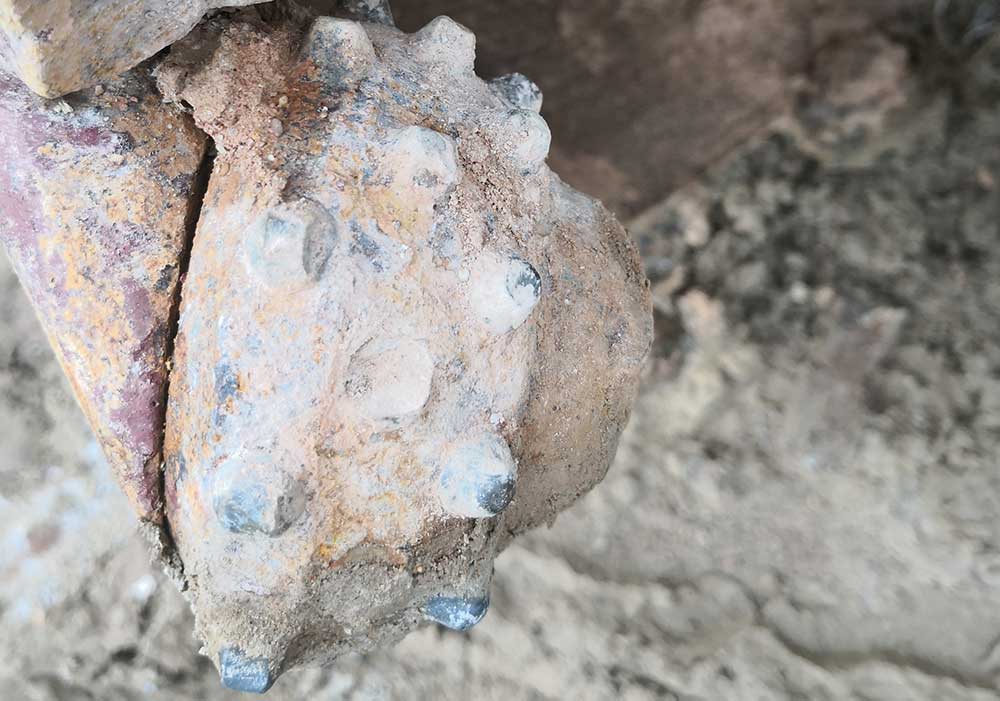
5. Inserts quick wear out

Let’s talk about these 2 failures together.
Except the manufacturer uses unqualified tungsten carbide inserts and challenging projects, both of these 2 failures are likely caused by choosing the wrong insert shape and layouts.
The roller bit original designed for oil & gas application, which there is IADC code to demand the right inserts for the right hardness of formation. But when it comes to piling, people do not care it much. But these would be a problem.
Making tungsten carbide inserts is just like cooking. You put some gradients, it will come to harder, but crisper, and put another gradient, it will come to stronger, but softer.
So, choose the right inserts for the right rock is key to avoid these failures. FIRMTECH inserts layout is as following:
Chisel
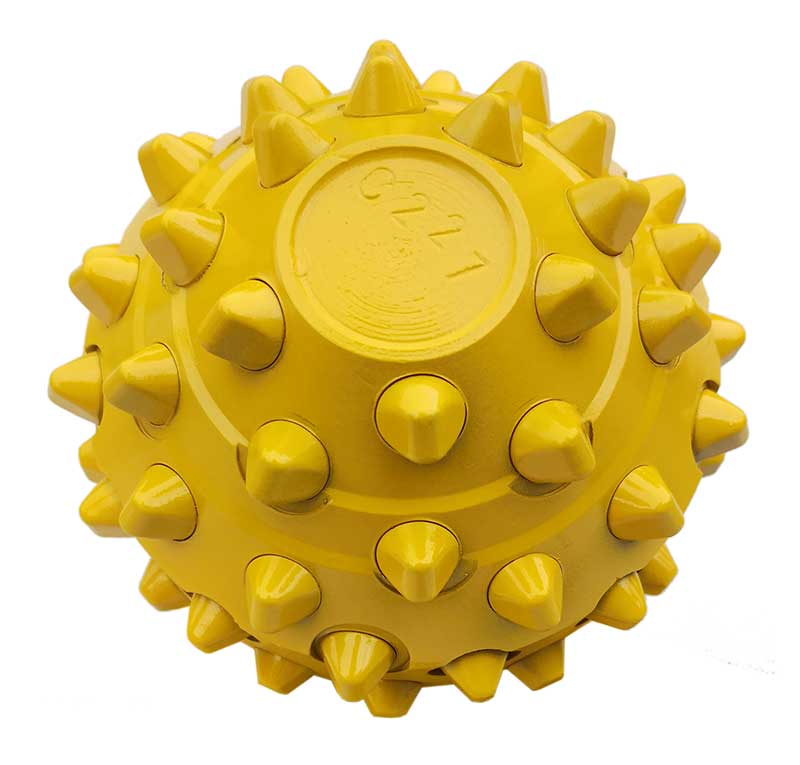
SOFT
100-120 Mpa
Conical
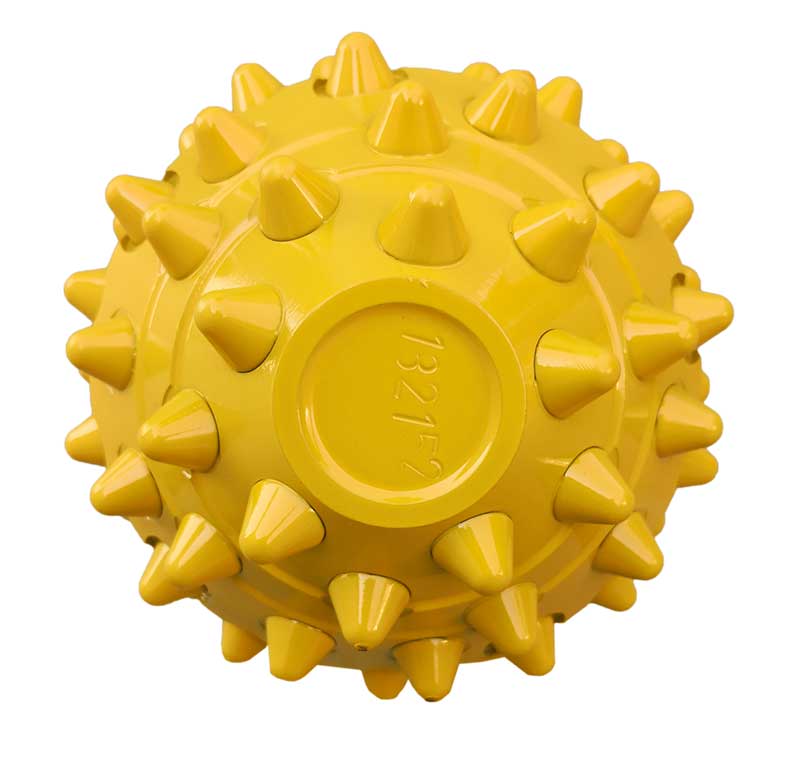
MEDIUM
120-140 Mpa
Ballistic
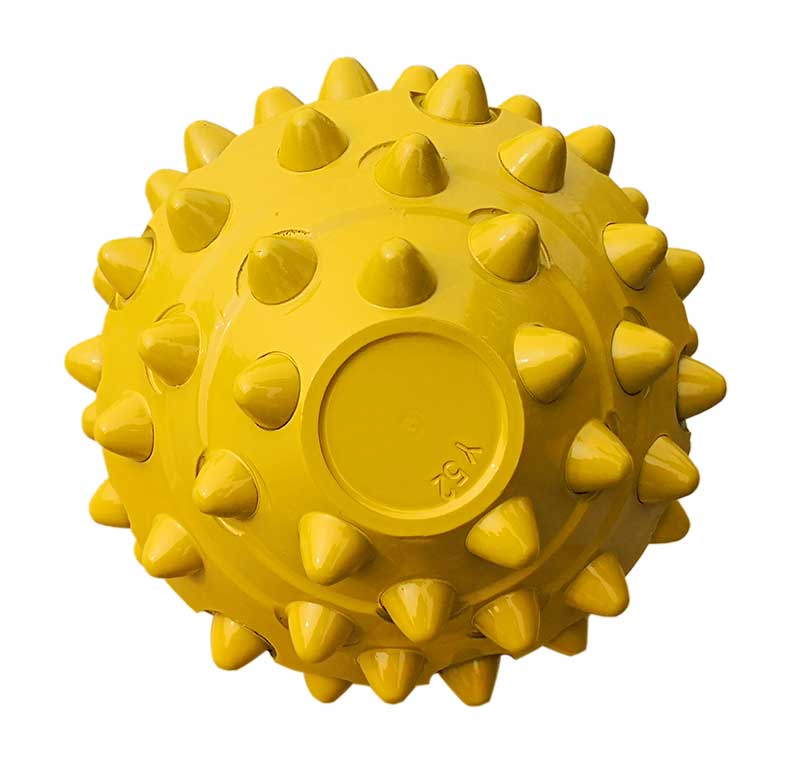
HARD
130-180 Mpa
Spherical

ULTRA-HARD
150-380 Mpa
It worth mentioning here: if the formation contains lots of quartz, which is highly abrasive material, the inserts wear out faster. If your project has a similar formation, please contact us for more help.
6. Lost inserts.
Lost inserts are a completely different story compared to the snapped inserts.
Most the lost inserts are due to roller bit quality.
- Sallow inserts plantation. Do you know around 3/5 inserts are rooted inside the cone. This will firmly attach the inserts. Some factories may plant the inserts shallow in order to save material cost. This will cause the lost inserts.
- Big tolerance on the hole drilling. The insert and the cone are attached according to interference fit. If the hole not precise, with big tolerance. The inserts are likely to be lost during the hard formation.
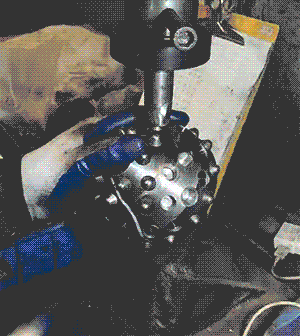
7. Broken Snapped Leg
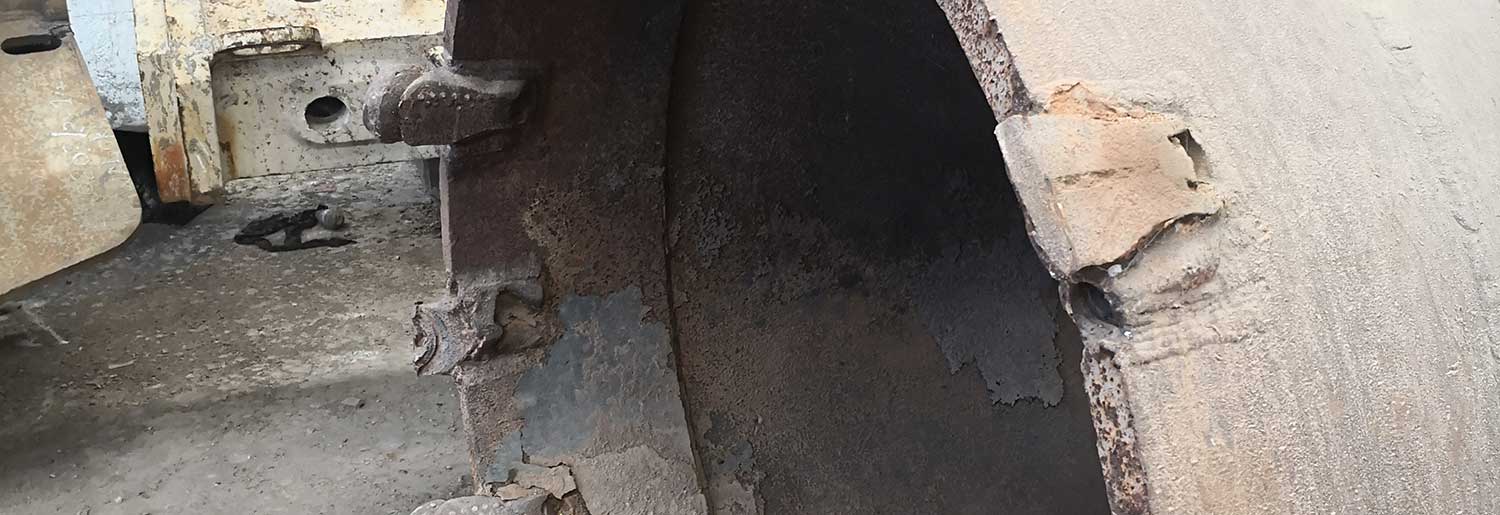
Sometimes the leg is just broken and lost in the middle.
For the roller bit quality perspective, this is caused by the bad forging.
All the roller bits made by forged alloy steel. If there is an internal injury during the forging, it may cause the snapped leg. (BIT)
Formation places a key factor too in this situation. If the formation is very uneven or piling in karst cave formation, that is, unfortunately, you got a very hard time. The roller bit simple will break by hardly hit on the rock. the snapped leg is barely inevitable.
In a nutshell, the piling on the hard rock can be very challenging .
With higher and higher competition on the deep foundation business, there are some many hard job and headache to deal with. But I believe choosing the right hard rock piling bit should not to be one.
A professional and full of onsite experience not only can prevent the problem happening in beforehand but also be a reliable source to count on the challenging job. In order to save you more money and time to work on something really matters.