We all know how trick it can be when comes to use a Core Barrel Roller Bit. Using roller bit is not like using the bullet teeth, while bad welding can make the whole expensive tools scrapped without even into the piling hole.
The following 7 points can help you weld and replace our core barrel roller bit confidently.
1. Cut the right gap
Cut gap on core barrel at proper dimensions, gap-width should not be left too big. Half to 2/3 height of cones should be out of barrel-top after welding. Steel plates on two sides of the cones should be chamfered.

The half hide cone is mainly to protect the body snapped when piling extreme uneven formation.
2. Always use even numbers
3. Right angle
The angle of the welding roller bit should be position as 5-6 degree. This is to protect the vulnerable shirttail place and maximize the cutting surface.

4. Same flat & circle
Keep all cones at the same height and same round circle, protruding roller bit will be broken easily.
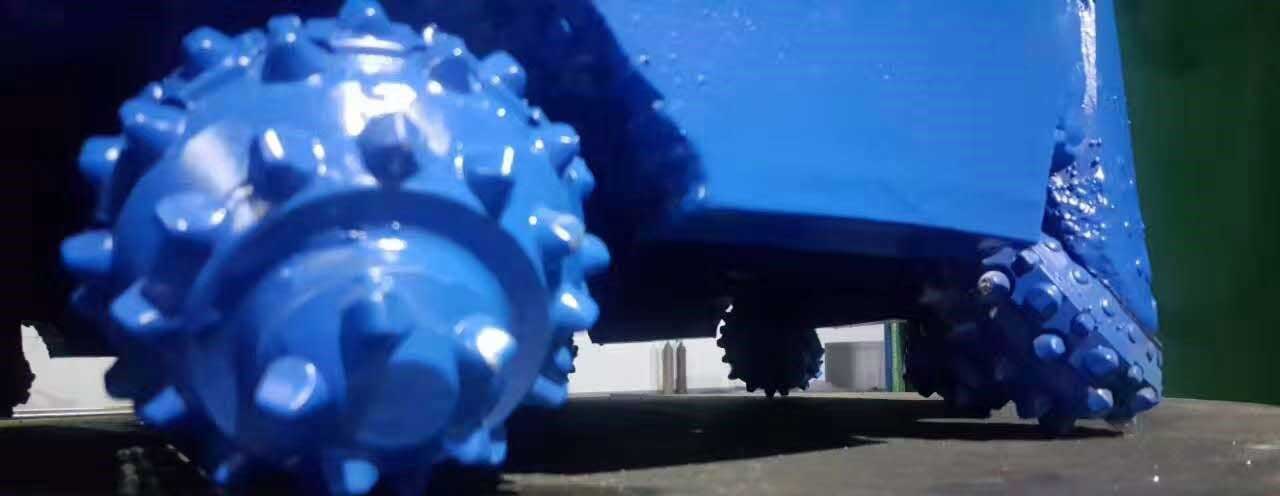
5. Right distance
The outward and inward roller bit should overlap to the right position ( the most outside point on the outward bit to the most inside point on the inside bit should be 120mm-140mm), otherwise the inner circle of the roller bit will be worn out quickly.

6. Cooling down
7. Welding by steps
Roller bit should be welded evenly and slightly to fix the position, then apply the full welding, otherwise the roller bits and angle will change.