With working with our most professional client, traveling to operation field, FIRMTECH team found out one of the most common issue which lead to bore pile roller cone bit lost Cone: Shirttail Part Wearout.
Actually, this problem has happened for years and it always the main reason to prevent a better roller bit working life. It is a top criminal to affect the client hard rock project profit and efficiency.
We have been doing a special research on how to do more on product, welding and operational point to reduce this Shirttail Part Wear-out.
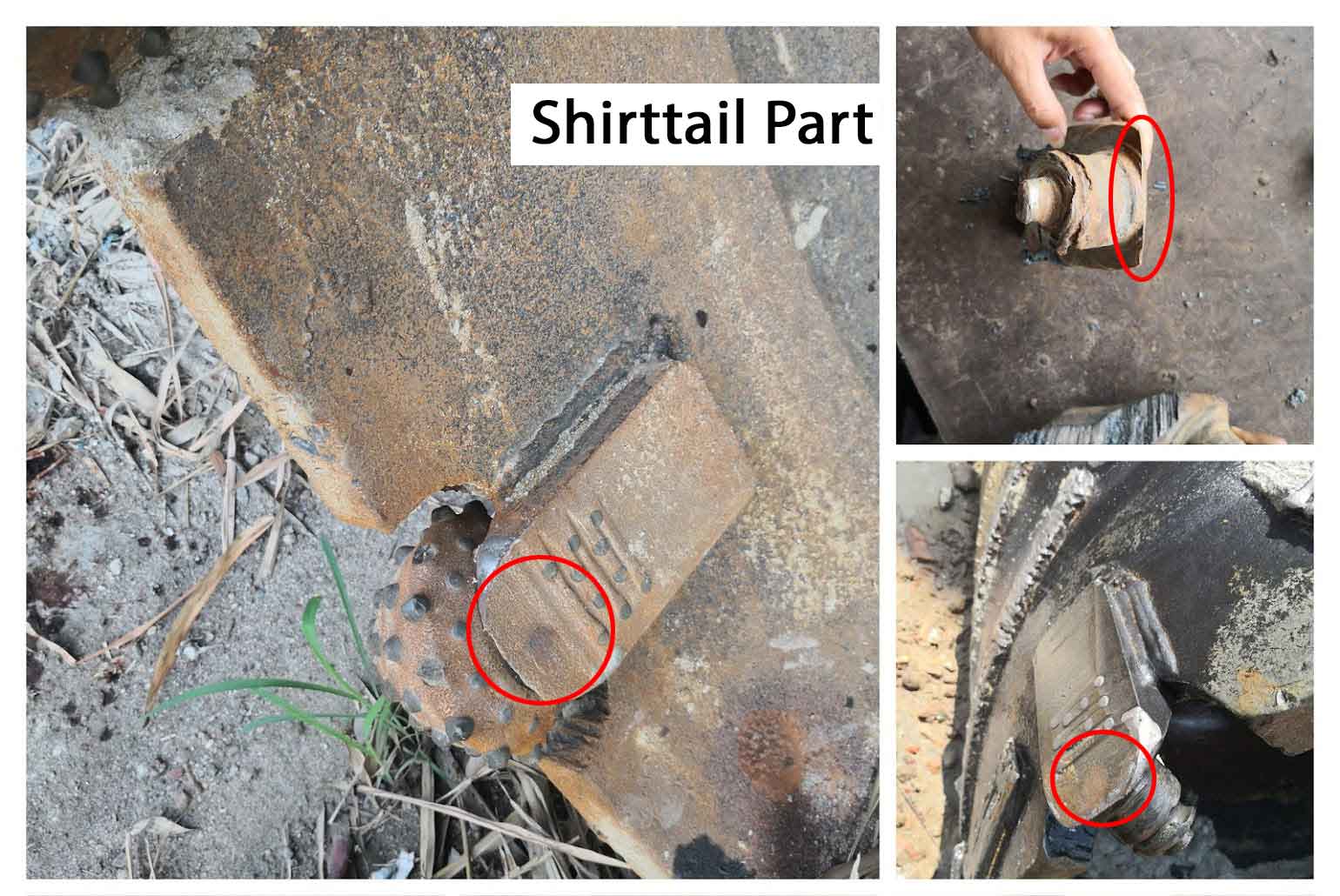
Shirttail Part has been a weakest point on the roller bit because the nature design. There are 2 reasons:
- Shirtail part is the thinnest part on the roller bit leg. It is as thin as a blade, easy to wear-out. And because it is so thin that can not be planed with inserts like the leg back. It is hard to protect it.
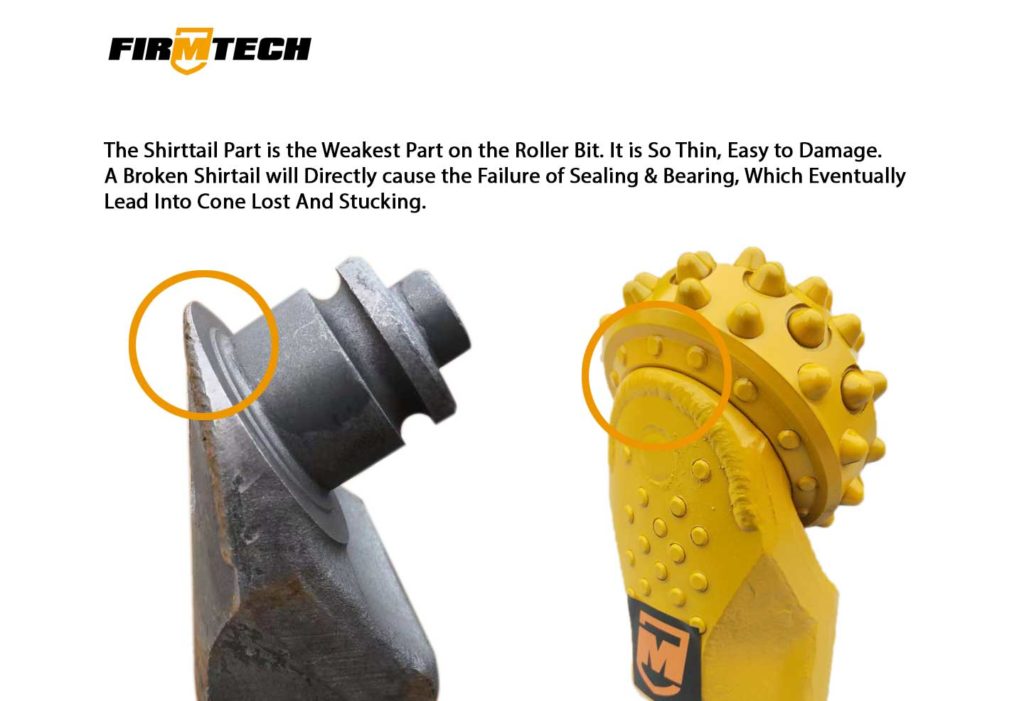
2. Shirtail part is the key spot to protect the sealing system. The dust and slurry can get to the bearing easily once the shirtail damaged.

What Caused the shirtail wearout?
There are mainly 3 reasons:
- Borehole Diameter Shrinkage
- Second time breaking, rock debris wearing
- Not properly Welding Angle
Borehole Diameter Shrinkage
Borehole diameter shrinkage happens time to time because various reasons including challenging formation, wrong operation & bad tool.
When the shrinkage happen, the some drilling load will change from vertical into horizontal to push the roller bit into the center of core barrel. The rock will touch the back and shirtail part of roller bit hardly. If the operator continue to drill as the same weight, the shirtail part will wearout easily to make the roller bit failure.
We suggest to lower the drilling weight, smoothly drill and pass this shrinkage phase, then to continue.
Second time breaking & rock debris wearing
Roller bit firstly designed for oil & gas industry. They are used with a hydraulic system to remove the debris when it is drilling.
But for piling application, most of the time, there is no such a system to help to get of the debris. So they will covered with roller bit once it breaks the rock first time.
This small pieces rock and debris will drage the cone and consitance wearing the inserts and shirtail part. Specially when it contains high abrasive material like quartz.
And this covering sometimes make the working surface too hot too. Increase the bearing failure.
There is a type of core barrel design good for this situation as following:

The flat teeth on the bottom will remove the debris along with the spiral sheet on the core barrel drum. This will make a relatively clean bottom surface to increase the drilling efficiency.
Not properly welding angle
We suggest to make 5-6 degree angle for FIRMTECH roller bit when do the welding. (Different brands suggesting angle may vary.)
The meaning of this angle is to put the most of cutting inserts touching with the rock, and avoid the gauge inserts and shirttail part rock contact.
Improperly angle (too big or small) will affect the roller bits performance by damaging the shirttail or inner part of bits. Eventually cause cone losing or stuck.

What FIRMTECH does different to tackle this problem on product side?
We are improving our roller bit constantly, and will do so for this special issue as same.
We are doing 3 changes to make FIRMTECH shirttail as strong as possible. To leave more freedom and room on the operation and facing the challenging formation.
1. Make the thicker shirttail part
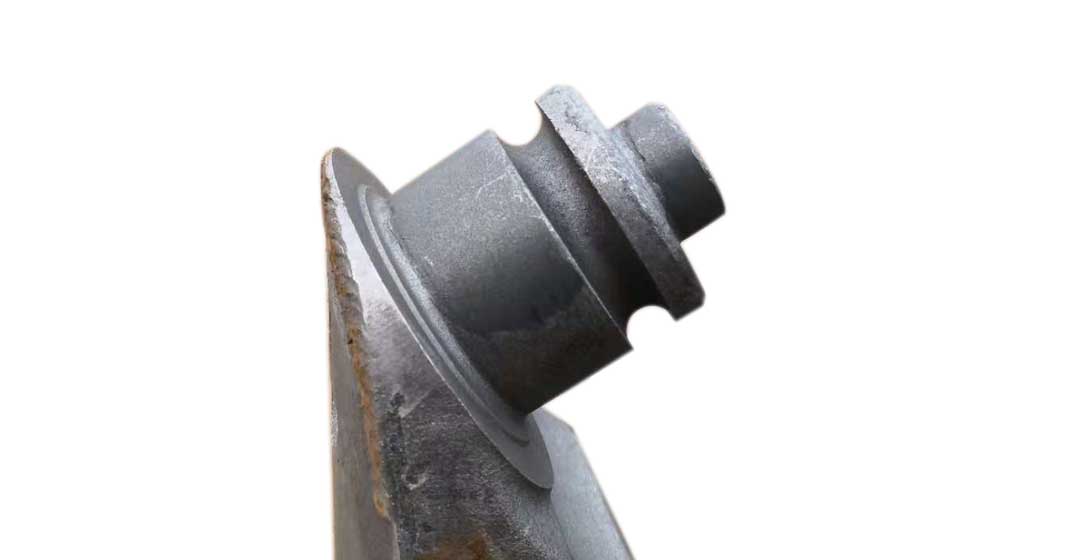
2. Double Thickness hard-facing. Best anti-resistance material applied.

2. Double Thickness hard-facing. Best anti-resistance material applied.
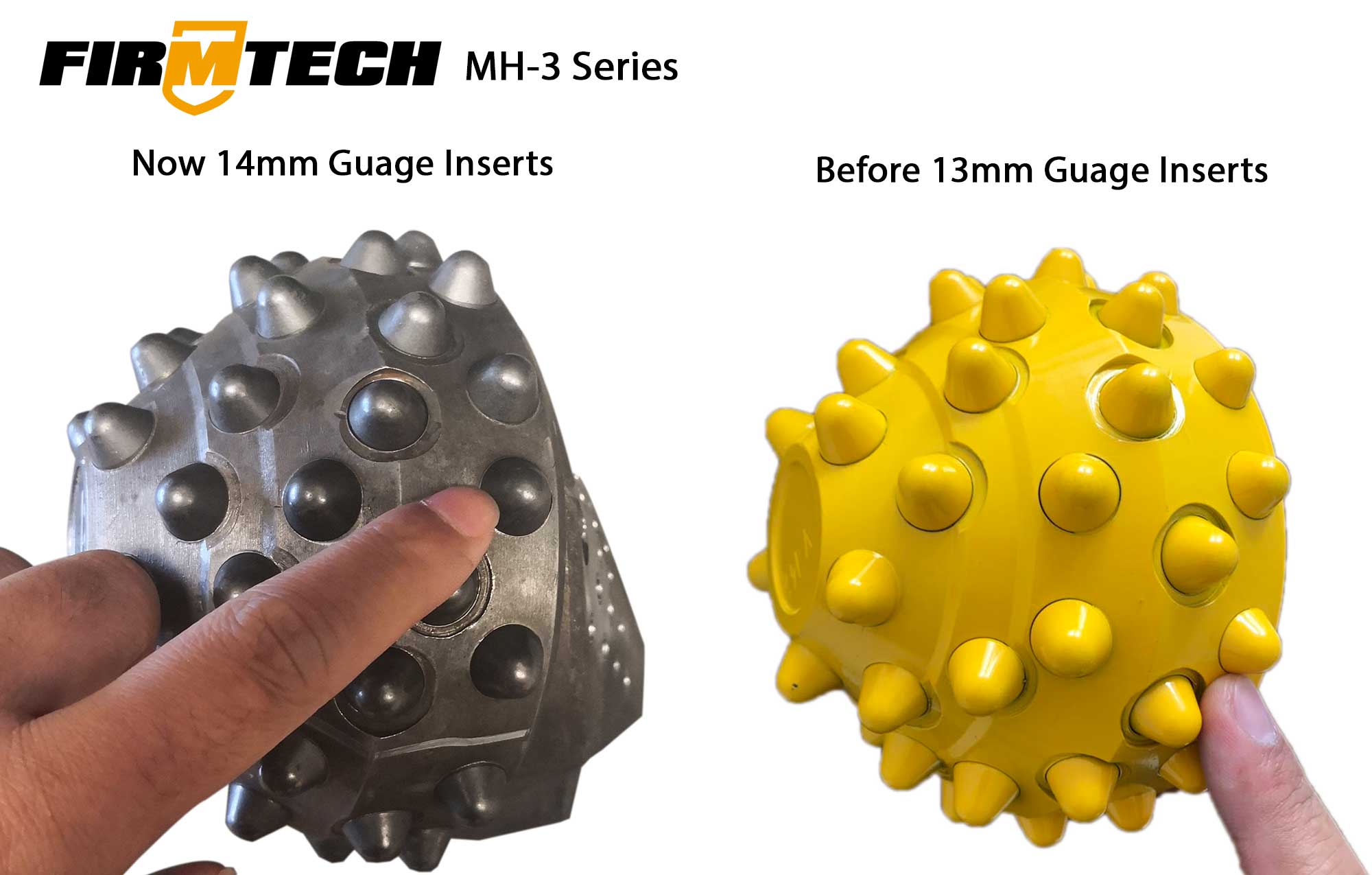
FIRMTECH Roller Bit
The roller bit has been used in the below formation:
1.5 Diameter, 2-3 meters socketing each pile, after 4-5 piles used. RQD 85%+, UCS 120Mpa, Granite.
The condition is still great, ready to use more.